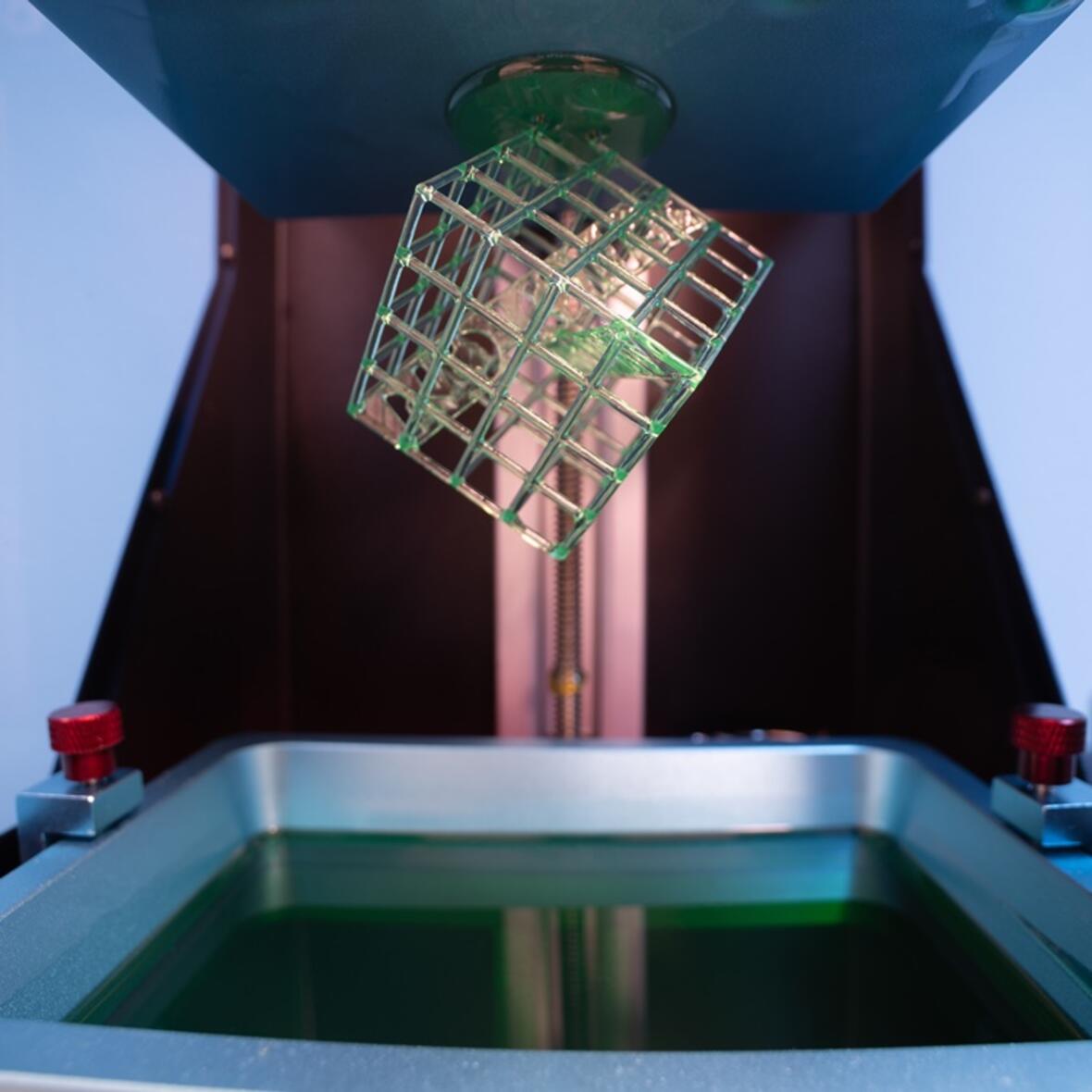
The basic principle of both the SLA and DLP processes is the selective layer-by-layer curing of a photopolymer by a light source. In the SLA process (stereolithography), a (UV) laser is used for this purpose. The laser beam is directed via movable mirrors to the corresponding points one after the other, where it selectively cures the liquid photopolymer. The DLP (digital light processing) process uses a projector or LCD display as a light source instead of a laser, projecting an image of the entire layer to be cured. In this way, all dots of a layer are cured simultaneously, which means that the printing speed with the DLP process is normally significantly faster than with the SLA process.
Short production times together with high precision and surface quality enable the application for prototyping as well as the production of casting molds, filigree models and small series in many areas of industry and medical technology.
The photopolymers used are light-curing synthetic resins based on epoxy and acrylic, or more rarely vinyl.
The use of functional fillers such as Neuburg Siliceous Earth offers the possibility of adjusting the mechanical properties of the cured photopolymers.
The aim of this study is to present Neuburg Siliceous Earth as a mineral filler for light-curing 3D printing resins (SLA/DLP).
The mechanical properties were tested in an acrylate-based resin formulation.
ADVANTAGES OF USING NEUBURG SILICEOUS EARTH
- despite fill level up to 20 %
- largely retention of tensile strength, elongation at break and impact strength
- moderate increase in viscosity
- increase in stiffness and heat distortion temperature
- undisturbed UV crosslinking